Spiral Freezers
•
Cryogenic spiral freezers
• Mechanical spiral freezers
• Cryogenic spiral freezers convertible
into mechanical spiral freezers
Freezing
Tunnels
• Continuous in-line I.Q.F. freezing tunnel
• “Cryofood” cryogenic freezing
tunnel with trays
• “Cryofood” mechanical freezing tunnel with
trays
• Quick-freeze linear tunnels
Freezing
Chambers
• Mechanical freezing chambers
• Cryogenic freezing chambers
------------------
•
Leavening
• Pasteurization
• Baking
• Protection
• New Production Lines
|
“Cryofood”™
Type Mechanical Tunnel Freezer
Technical
characteristics
This type of system is built in a rather different manner
compared to traditional mechanical systems, and provides
the following advantages:
a) it saves much of the refrigerating potential. This
is due to externally mounted motors driving all of the
fans, including those installed inside the chamber. This
way, no refrigerating potential is drawn from the freezing
process.
b) Format flexibility. If needed, the working distance
between two trays can be doubled by simply extracting
some of the trays (every other tray) and synchronizing
the feed rate again
c) Compact size. Given its interesting output capacity,
the size of the machine – basic overall dimensions
in particular – is rather small. The distribution
of volumes has been optimized thanks to accurate engineering.
Functional description of machine
This system is used to obtain the rapid freezing (deep-freezing)
of products arranged on trays.
Machine operation is very simple.
A chain device allows trays to advance automatically,
from the loading area onto a track that runs along the
refrigerated box, and up to the product unloading area
after the product has been frozen. |
The
trays move along the following route:
• arrival from the previous processing station (oven
or cooler)
• freezing cycle
• unloading or transfer to other processing stations
|
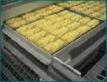
|
At
the end of this track, trays are automatically brought
back to the loading area.
The track runs along a closed circuit; this means that
trays never leave the machine, so there is no need to
move them manually.
The trays move along the following route:
•
loading
• rapid freezing cycle
• unloading
return to loading area
all
is done automatically and without the trays ever leaving
the work cycle.
|
Two
motor speed variators placed outside the refrigeration box
transmit motion to the conveying mechanism, so product stay-time
in the freezing box can be adjusted according to product
freezing time requirements.
The cooling of the isolated chamber is obtained by using
cold energy of adequate power to cool an evaporator situated
inside the chamber and placed above the tray feeding system.
The inside of the chamber is highly ventilated to facilitate
the quick freezing of products; heat exchange between air
and product occurs at a speed of approx. 3 metres/second
throughout the chamber.
The evaporator is equipped with an automatic quick defrosting
system that melts any ice formed by humidity condensate.
Defrost water is channelled outside the chamber. |
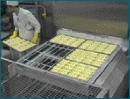
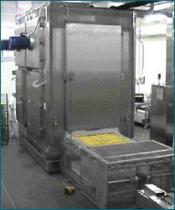
|
Cleaning and defrosting at the end of the work cycle are
easy to perform because the box is provided with a door
which gives the operator full access to the inside of the
machine.
To make maintenance or access to the upper parts of the
system easier, the machine is provided with a gangway that
surrounds the construction about 3 metres above ground,
complete with banister and stepladder, all in accordance
with applicable health and safety regulations.
The machine is manufactured in accordance with applicable
regulations and is supplied with a certificate of conformity
with European Directive EEC 89/392.
|
|