Spiral Freezers
•
Cryogenic spiral freezers
• Mechanical spiral freezers
• Cryogenic spiral freezers convertible
into mechanical spiral freezers
Freezing
Tunnels
• Continuous in-line I.Q.F. freezing tunnel
• “Cryofood” cryogenic freezing
tunnel with trays
• “Cryofood” mechanical
freezing tunnel with trays
• Quick-freeze linear tunnels
Freezing
Chambers
• Mechanical freezing chambers
• Cryogenic freezing chambers
------------------
•
Leavening
• Pasteurization
• Baking
• Protection
• New Production Lines
|
Cryogenic
Spiral Freezers
Technical
description of the system
The cryogenic spiral freezer comprises the following units:
|
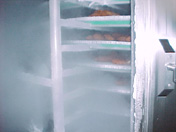 |
• An insulated enclosure where the
freezing process takes place
• A conveyor belt placed inside the enclosure for
the continuous conveyance of products
throughout the freezing procedure
• A ventilating, regulating and cryogen suction
centre
• An automatic conveyor belt washing system
An electric control panel housing the system’s centralized
control
|
The
enclosure consists of a one piece construction
with a stainless sheet steel double wall with 150 mm thick
self-extinguishing polyurethane foam insulation.
This type of construction, besides providing unlimited
durability, also prevents any water seepage or filtering
of contaminants through the walls hollow spaces. The enclosure
is provided with manual doors giving full access to all
inner parts of the spiral, making cleaning operations
at the end of the work cycle easy and quick to perform.
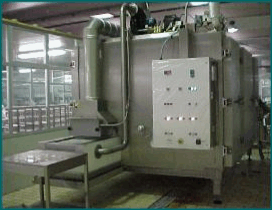
|
The
conveyor belt is located inside the enclosure and
moves along a closed circular loop that winds in spiral
around a rotary drum.
The cryogen gas regulation and suction
centre consists of a modulating valve with proportional
opening features. The modulating valve controls the flow
of cryogen liquid into the freezer. The operating freezing
temperature inside the spiral box is about –60°/-70°C.
A proportional digital thermostat regulates the temperature.
Adequate ventilation is provided all along the belt circuit
to ensure efficient heat exchange with the product.
Spent gases are sucked in via the product in feed and out
feed openings and are directed to an external exhaust. |
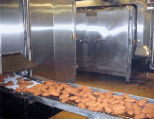 |
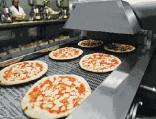 |
The
automatic belt washing system is located externally,
in the product loading area and consists of a pipe that
feeds a series of spraying nozzles fed by a high pressure
electric pump.
Washings collect in a tub under the spraying ramp and
then flow into the water drain.
The
electric panel is equipped with all the accessories
required to assure a fully automatic control of the process,
both via electromechanical controls and via PLC. |
|