Spiral Freezers
•
Cryogenic spiral freezers
• Mechanical spiral freezers
• Cryogenic spiral freezers convertible
into mechanical spiral freezers
Freezing
Tunnels
• Continuous in-line I.Q.F. freezing tunnel
• “Cryofood” cryogenic freezing
tunnel with trays
• “Cryofood” mechanical
freezing tunnel with trays
• Quick-freeze linear tunnels
Freezing
Chambers
• Mechanical freezing chambers
• Cryogenic freezing chambers
------------------
•
Leavening
• Pasteurization
• Baking
• Protection
• New Production Lines
|
Tray ovens for baking and pasteurising processes |
The changing production needs in foodstuff baking and
pasteurising insistently call for continuous cycle machines
that are capable of baking and pasteurising food at very
high hourly output rates. In view of this, we have added
to our refrigeration and freezing tunnel range a type
of tunnel capable of performing continuous pasteurisation
and baking of any food product (to be conveyed either
on trays, or loose on a belt).
These tunnels can also be integrated within existing refrigerating
tunnels on the same line, so after the pasteurising and
baking process the product is automatically transferred
to the next processing cycle, into another tunnel where
it is cooled or frozen.
In making this new tunnel, we have used all our twenty-year
experience as seasoned manufacturers of infrared and hot
air heating and sterilising tunnels (of which, about 120
have been sold to the most prominent pharmaceutical undertakings
in the world).
Because of our vast experience as manufacturers in the
heat field we are able to obtain the best possible temperature
uniformity throughout the tunnel’s hot chamber,
thus we can meet any pasteurising or baking requirements,
from the simplest to the most complex.
The air heating process takes place inside an insulated
compartment above the tunnel’s hot chamber and is
carried out by means of a heater that is equipped with
a burner. This burner can be supplied with gas oil or
– if customer requests so – with other gases.
Recycled air will not come into direct contact with the
flame, but is heated by the high temperature that forms
inside the high-performance section of the furnace pipes.
Temperature uniformity is obtained thanks to two plenums
– a delivery plenum and a return plenum –
that fully cover both vertical, opposing walls in the
hot chamber. Air distribution in the tunnel chamber is
obtained by means of a horizontal laminar air flow system
and is uniform throughout, on all chamber surfaces.
The system is built in such a way as to ensure that when
the doors are open, all the tunnel inner areas are accessible
and easy to clean at the end of each working cycle.
Highly efficient insulating methods and high-density rock
wool have been used to insulate the walls.
Functional description of the machine
Machine operation is very simple: |
The
trays inside the hot chamber are fed by means of a chain-based
device that picks the trays from the loading area, carries
them along the heated and baking circuit and to the discharge
area.
The circuit is a closed loop circuit and each tray moves
along the following route:
o automatic feed into the oven
o heating or baking cycle
o automatic discharge of tray from the oven
Two motor speed variators placed outside the oven transmit
motion to the conveying mechanism, so product stay-time
in the hot chamber can be adjusted according to product
baking time requirements.
The system features an automatic tray washing and drying
station.
Both cleaning and maintenance of all the inner parts of
the oven are easy to achieve; the system is equipped with
two doors on opposite sides that make the inner parts of
the oven easily accessible.
The machine is manufactured in accordance with applicable
regulations and is supplied with a certificate of conformity
with European Directive EEC 89/392.
Before shipping, the machine is divided into two parts.
It is reassembled at the customer’s facility. This
is done in order to reduce the height of the machine, which
would otherwise need to be handled as special carriage.
|
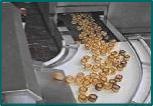
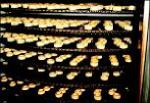
|
|
|
|